Steelpark is the UK’s largest steel distribution and processing centre, and the only one to be supported by a domestic steel mill.
Based in Wednesfield, West Midlands, Steelpark specialises in distribution and processing. With a complete multi-metal and full-finish capability, including decoiling, slitting, blanking, press blanking and tailor welded blanks, our hi-tech service centre provides dedicated processing and services for OEMs and tier suppliers. Our Profiling Centre's unique combination of oxy-gas, high-definition plasma and laser steel plate profiling capabilities, combined with state-of-the-art flattening presses, machining centres, edge finishing and press brakes, provide an integrated offering you can rely on.
Supplying an extensive range of sheets and blanks of cold rolled, metallic coated and hot rolled specifications, our large-scale decoiling facilities bring the benefits of excellent flatness and surface presentation to customers in the sheet metal and light engineering markets.
Our state-of-the-art facilities supply slit steel coil to customers in the construction fit-out and light engineering markets, providing a responsive, efficient and friendly service. Our dedicated automotive facility at Steelpark has a capacity in excess of 200,000 tonnes of processed steel per annum and offers a complete multi-metal (aluminium) and full-finish capability across the widest range of processes.
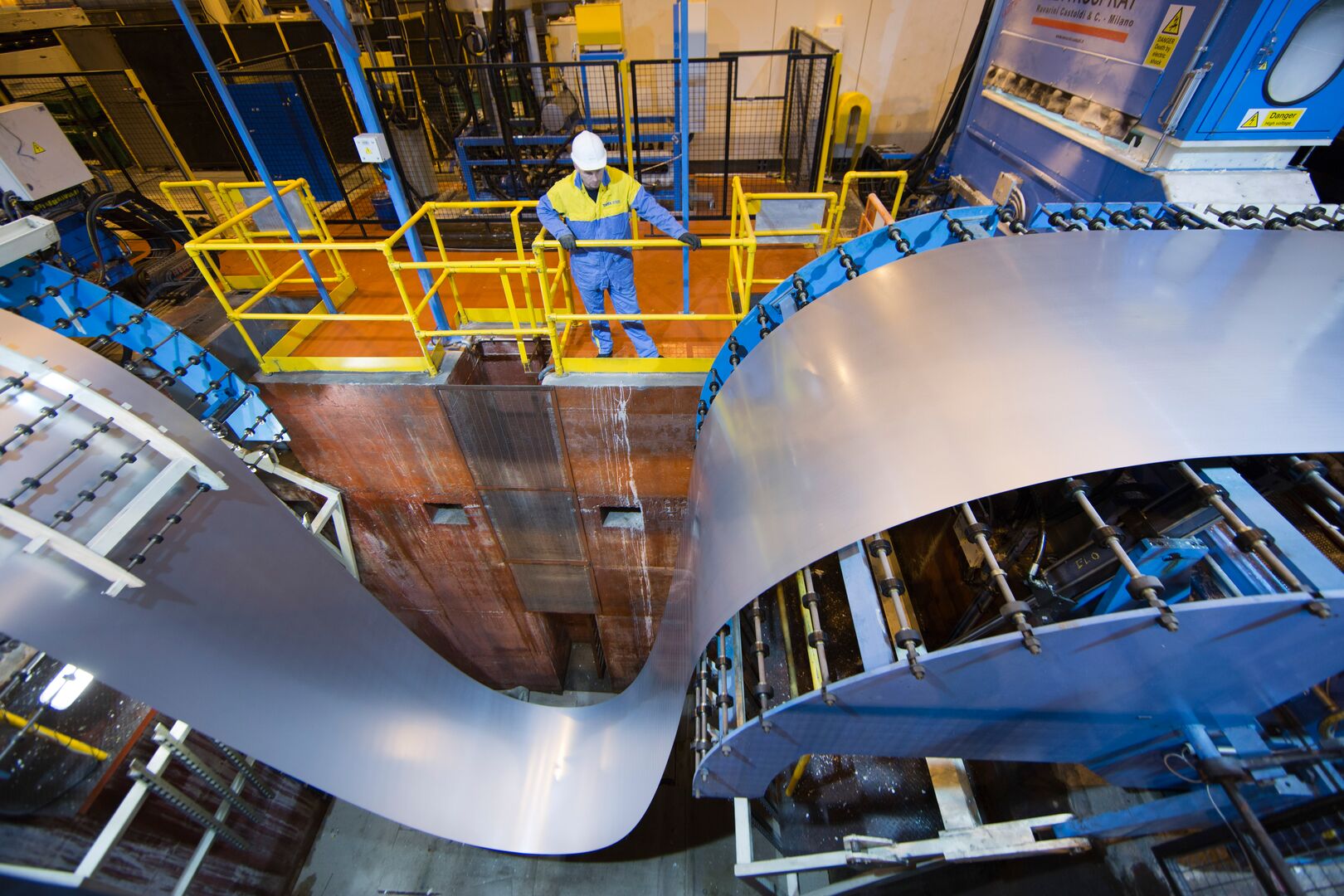
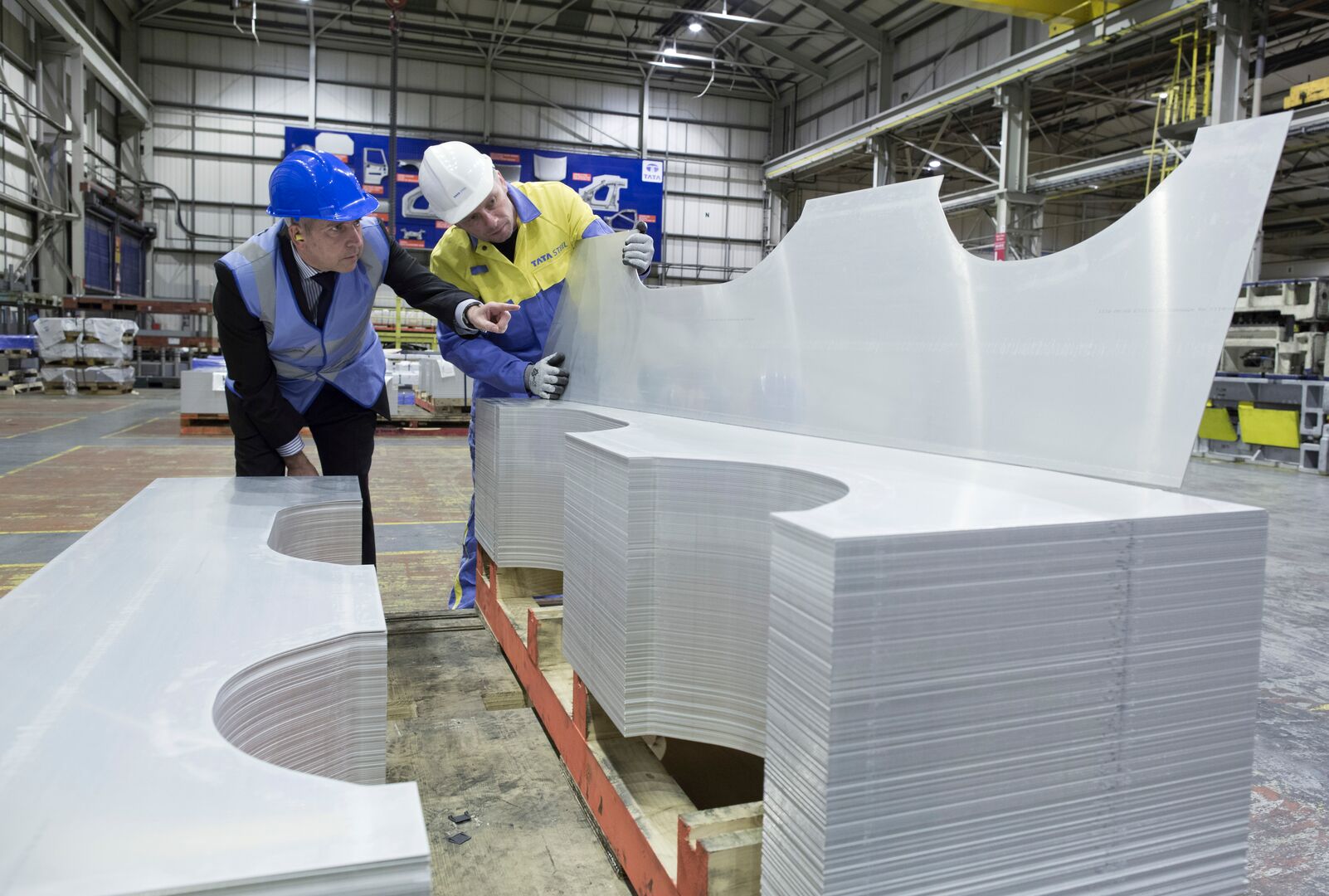
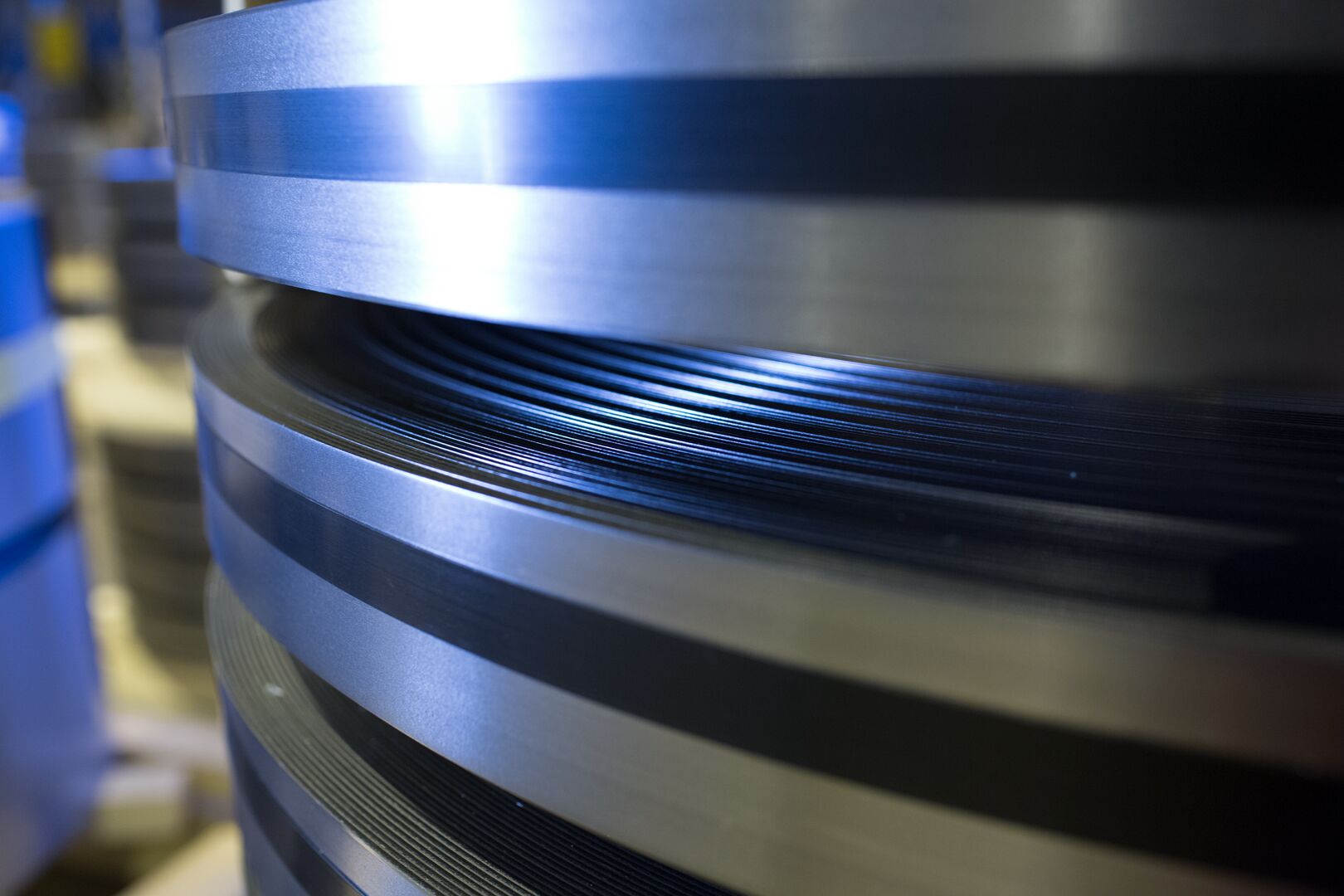
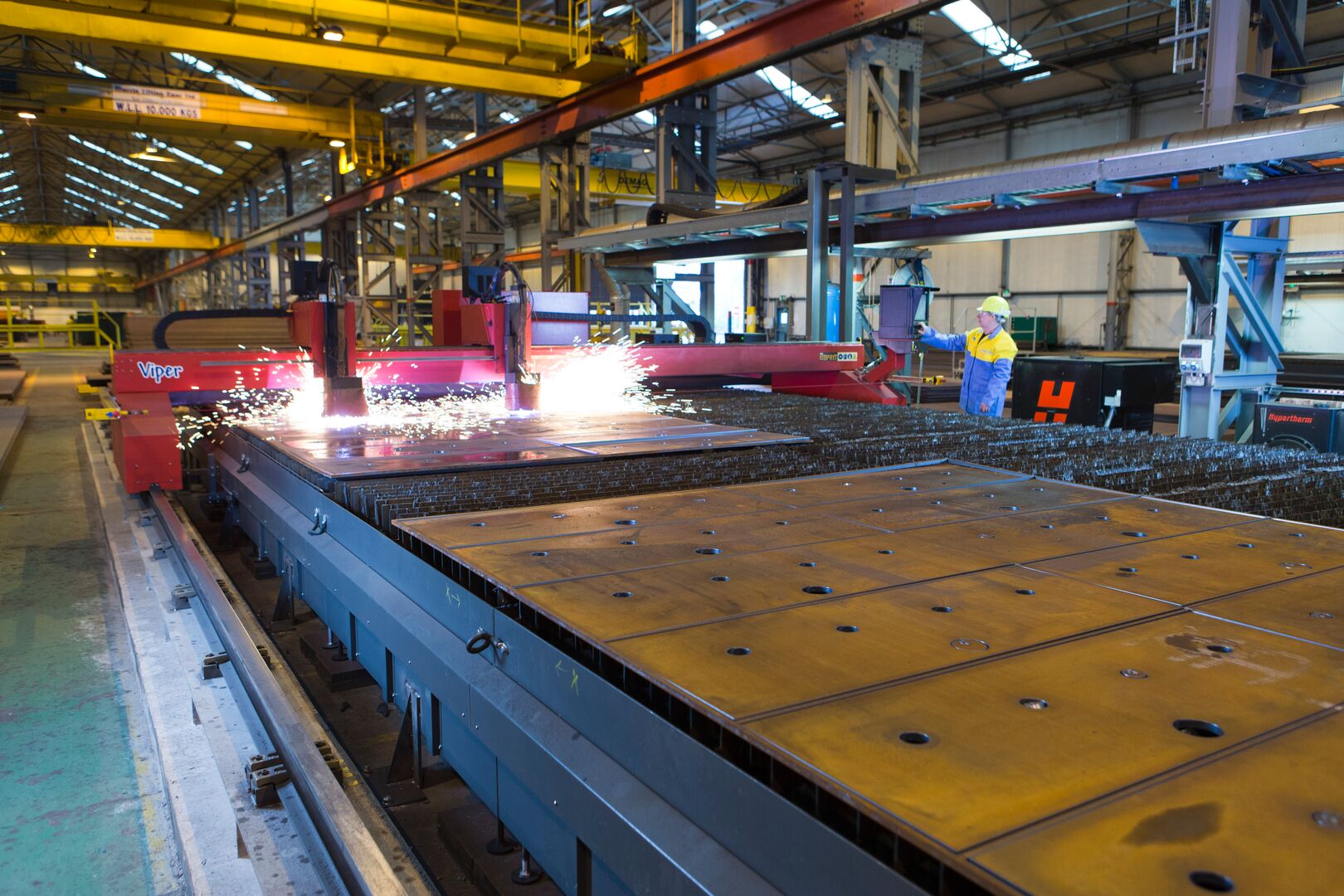
Our Light Gauge service centre at Steelpark focuses on the supply of flat sheet for a wide variety of market applications in the sheet metal fabrication and light engineering segments. Our slitting facilities supply slit steel coil to a multitude of customers in the construction fit-out and light engineering market. Located at Steelpark near Wolverhampton, it employs three highly-productive multi-strand blankers, a large dedicated decoiler for sheet production, four large slitting machines and a dedicated unit for the slitting of narrow coil. It processes the full range of Tata Steel cold-rolled, metallic-coated and hot-rolled coil specifications.
Customer benefits
Light Gauge Decoiling – Steelpark offers a range of benefits:
Repeatable processing. As part of a UK-based supply chain, we benefit from the consistent product quality of Tata Steel’s modern manufacturing sites at Port Talbot, Llanwern and Shotton. This ensures a repeatable processing experience for our customers. The majority of coil is supplied from South Wales via our own Round Oak rail terminal a few miles from the Steelpark, as part of a lean supply chain.
Security of supply. We offer a unique combination of three highly-productive multi-strand blankers and a large dedicated decoiler for sheet production, all located under one roof. It means we can provide customers with secure supply and sufficient capacity to support your growth plans - without compromising service.
Choice and savings. As well as supplying sheets and blanks, we also have the capability to shear in the same facility. This provides customers with a wide choice of blank size and shape, saving cost and time in further processing.
Tailored products. As an extension of the producing mills’ supply chain, we are able to interact with our manufacturing, technical and R&D colleagues regarding product specification. We can access the full range of steel grades, finishes and dimensional tolerances to develop unique specifications best suited to a particular application.
Supporting activities
Light Gauge Decoiling - Steelpark benefits from a number of supporting activities and features to provide customers with an optimum solution.
- Integrated supply chain. Light Gauge Decoiling is part of an integrated supply chain. We make steel in Port Talbot or IJmuiden and roll it in Llanwern, Port Talbot or IJmuiden. The steel is galvanised in Llanwern or Shotton, before slitting and decoiling at Steelpark. Visibility of customer requirements and demand through the supply chain allows stock levels to be managed to meet demand effectively.
- Full product traceability. The Tata Steel supply chain ensures we are able to manage product traceability effectively from primary production through to despatch.
- Product development. As one of the world’s largest steel producers, Tata Steel is able to offer customers an increasing range of innovative products. As part of our aim to supply differentiated products, we are launching up to 50 new products each year. Examples include highly formable and high-strength steels and novel coatings. We have also developed additional processing services.
Tata Steel is the leading steel processor and distributor in the UK and Ireland, giving customers access to:
- A complete product offering. Tata Steel manufactures an extensive range of steel products, including hot-rolled, cold-reduced, and coated products. We have the ability to supply whatever you need for your particular business.
- Best-in-class processing facilities. Our service centres have benefited from significant investment, resulting in best-in-class facilities across an array of processing technologies. We offer: the latest plate profiling and machining centres; high capability slitting, decoiling and blanking of strip products; latest automotive processing facilities including press blanking and tailor welded blanks.
- In-depth industry knowledge. Tata Steel service centres serve more than 6,000 individual customers each year. Our extensive experience of steel products, processing and applications can be utilised to support the development of your business.
Steelpark can provide a number of services to complement our best-in-class processing capability.
- Liaison engineers. Our liaison engineers have detailed knowledge of our products and processes and how they interact with those of our customers. It means we can provide responsive support, helping to resolve material and processing issues quickly. Our engineers also provide guidance on product specifications and the introduction of new products.
- Supply chain. We are experienced in the management of Kanban/JIT and other supply arrangements. We utilise complete IT systems that allow you to focus on your own processing activities with peace of mind regarding security of supply. Our 24-hour operations support flexible and regular delivery schedules on a nationwide basis.
- Matching your requirements. As part of Tata Steel, direct access to our own manufacturing facilities allows greater choice of both surface texture and surface finish. This means we can provide the best match for your processing and coating requirements. In addition, chrome-free passivation (HDG) is available for compliance with application-related market standards.
- Packaging. Processed material can be presented in your preferred orientation and packing type - ensuring ease of handling and subsequent processing in addition to safe loading and transport.
Processing
We undertake a full range of processing activities focused on the needs of the automotive supply chain. Our service delivers product, cost and further processing benefits to customers. In addition to precision slitting and decoiling, highlights of our capability include tailor welded blanks, press blanks and blanking.
Tailor welded blanks. We operate the very latest tailor welded blank technology, capable of producing complex two-dimensional/non-linear weld geometries. This provides designers with a greater degree of freedom to create:
- weight-saving opportunities
- cost-reduction possibilities
Our capability is particularly relevant for parts such as door inners or larger body side blanks. We use the most appropriate steel grade in the right place and at the right thickness. Without compromise to structural performance, our engineered blanks:
- optimise material use
- minimise post-joining operations
- reduce overall tooling costs
One of only a few in the world, our new high speed 1-dimensional line will treble the amount of parts we can produce for our automotive industry customers across the UK and Europe. It is our second TWB line for Tata Steel's Wednesfield site and is part of our long term strategic aim to be the partner of choice for our customers.
TWB’s allow the use of the most appropriate steel grade in the right place and at the right thickness therefore optimising material use and minimising post-joining operations. Our TWB lines can join up to 5 individual shaped blanks of differing material grades and thickness, allowing panels to be optimised for weight and cost.
Following a £4million investment, our new line marks a step change in what we can provide for customers in the automotive industry.
Take a look at the new TWBL video:
Want to get closer to our new TWB facility? Find our 360 virtual reality tour here.
(VR enabled, you can also view it with your Google cardboard headset)
Press blanks. We currently operate five different press blanking lines from 150-600 tonne capacity and of varying size. Press blanks offer customers potential cost reduction and productivity improvements through:
- enhanced part nesting
- reduction of in-process scrap handling
- re-deployment of floor space and press capacity for additional production
- lowering of inventory costs through supply chain management
In response to customer demands, we have invested to create a multi-metal processing capability. This has purpose-designed process sections dedicated to either steel or aluminium. It also includes a novel coating section able to apply customer-specific solutions to blanks - to aid subsequent pressing.
Blanking. With a total of seven different blanking lines, we are able to produce square, rectangular, trapezoidal and radial blanks of an almost limitless configuration. Additional multi-stand blanking lines located at Steelpark ensure we are able to provide the flexibility and capacity to respond to customer requirements.
Services
We can provide a number of services to complement our best-in-class processing capability.
Product packing. We are able to present our products in the most convenient orientation for subsequent processing. We offer:
- use of bespoke or customer-own pallets
- utilisation of pack turners to configure left- or right-handed parts
- application of ‘dimples’ to blanks to aid separation and handling
- specific wrapping materials
- Liaison engineers.
Our liaison engineers have detailed knowledge of our products and processes and how they interact with those of our customers.
Our engineers are available to work closely with customers from the earliest stages of a project (EVI)– offering significant experience in new part introduction and project management.
Tool design and management. Tata Steel works closely with leading toolmakers across Europe to undertake design, procurement and subsequent management of the tool fleet needed for your specific blanked parts.
Supply chain. We are experienced in the management of Kanban/JIT and other supply arrangements. We utilise complete IT systems that allow you to focus on your own processing activities with peace of mind regarding security of supply.
The Plate Profiling Centre is a centre of excellence for the profiling of steel plate. It is located at Steelpark near Wolverhampton, one of Europe’s largest steel service centres. The Plate Profiling Centre operates as part of a unique supply chain extending right back to the steel mill. Under a single roof, the centre offers:
- the latest plate profiling technologies
- comprehensive finishing facilities
- access to the widest range of steel grades
Increased capacity and capability
After successfully serving the heavy vehicles segment from our former Cradley and Wombourne sites for more than 20 years, we have made a significant investment in the Plate Profiling Centre. Our investment - including installation of new high definition plasma profiling machines and machining centres – has resulted in:
- increased capacity
- extended processing capability
- operational flexibility – to meet customers’ current and future needs
- improved delivery service
Customer benefits
The Plate Profiling Centre delivers benefits to customers in a wide range of markets:
- Heavy vehicles. The centre is ideally configured for high-volume repeat part production for most machinery segments, including off-highway wheels. We have the capability to manage lean supply chains, providing kitting of parts ready for fabrication and just-in-time delivery.
- Construction. Structural components can be readily handled from large-area profiling beds and associated handling systems, for one-off projects or general applications.
- Energy & Power. Together with the Wind Tower Hub located at Scunthorpe, we are capable of profiling and handling the very largest of plates. To save you processing time and cost, we provide a wide choice of edge finishing as preparation for welding and further fabrication.
- Transport. Rail and road schemes are making increasing use of gantries and other fabricated structures, for applications such as line electrification, information systems and signage. Our profiling capability and capacity allows contractors to concentrate on their core fabrication processes. By supplying components, we can save our customers time and cost - removing waste from the supply chain.
- General Engineering. We can supply a multitude of parts for applications involving steel plate, from single-part prototypes to low-volume production runs.
Services
The Plate Profiling Centre can provide a range of services - saving you time and cost. These include:
-
JIT. By supplying parts on a ‘just in time’ or Kanban basis we can greatly simplify customer supply chains - and help you limit the resources tied up in stock and floor space.
-
Kits. We can combine selections of parts into kits. This ensures the exact required parts are presented to a fabrication or assembly process - removing the need for you to sort and aggregate parts from stocks.
-
Design. When customers share their part specifications, we are able to interpret the design and tolerances to ensure the most appropriate processing routes and part nesting. It means you benefit from the most efficient use of material and processing time. Utilising our economy of scale and scope can ensure customers receive the most efficient processing service.
Decoiling
Thickness | Width | Length | Comments | ||||
---|---|---|---|---|---|---|---|
Min (mm) | Max (mm) | Min (mm) | Max (mm) | Min (mm) | Max (mm) | ||
Decoiling | 0.7 | 3 | 900 | 2000 | 700 | 4000 | 2t pack weight |
Blanking | 0.35 | 3.2 | 600 | 2000 | 420 | 4000 | Minimum blank width = 150mm |
Up to 5 strands per coil width | |||||||
Shearing | 0.4 | 6 | 200 | 3050 | 200 | 2450 | Minimum blank size = 20mm |
Five high-accuracy shears |
Slitting
Slit width, min (mm) |
Thickness, range (mm) |
Comments |
---|---|---|
30 | 0.20 – 8.00 | Hot-rolled, Hot-rolled P&O, Cold-rolled, Metallic coated (inc. MagiZinc®) |
Steelpark Automotive processing
Processing unit | Width | Thickness | Comments | ||
---|---|---|---|---|---|
Min (mm) | Max (mm) | Min (mm) | Max (mm) | ||
Tailor welded blanks | 400 | 3000 | 0.6 (Steel) | 3 | Blank lengths up to 3600mm |
0.9 (Aluminium) | |||||
Press blanks | 210 | 2050 | 0.4 | 3 | 150-600t press capacity |
Stacking up to 5000mm length blanks | |||||
Blanking | |||||
- Trapezoidal | 400 | 1810 | 0.4 | 3 | Stacking up to 4500mm length blanks |
- Radial | 400 | 1680 | |||
- Square/Rectangular | 250 | 2010 | |||
Slitting | 34.5 | 2020 | 0.4 | 3.2 | Up to 30 individual slits across coil width |
Shearing | 50 | 2500 | 0.4 | 3.2 |
Plate Profiling Centre
We provides a full-service capability to plate-consuming customers. The configuration of profiling and finishing operations under a single roof ensures the most appropriate and cost-effective process route is employed for each customer’s requirements.
|
Plate Width, |
Plate Length, |
Plate Thickness, |
Comments |
---|---|---|---|---|
Oxy-Gas Profiling |
5700 |
20000 |
170 |
Best suited to profiling thicker plates |
High-Definition |
5000 |
20000 |
55 |
Outstanding capability from five machines |
Laser Profiling |
2500 |
8000 |
20 |
High precision cutting of lighter plate |
Flattening Press |
|
|
60 |
Flattening down to 2mm / m deviation |
Machining Centres |
970 |
2300 |
170 |
High precision finishing of profiled components |
Edge finishing |
|
|
150 |
Detailed edge finishing from one slag grinder |
Press Brakes |
3600 |
800 |
30 |
300t capacity press braking from two machines |
Designed to undertake primary plate processing for renewable energy applications, our Wind Tower Hub capability complements the Plate Profiling Centre.
|
Plate Width, |
Plate Length, |
Plate Thickness, |
Comments |
---|---|---|---|---|
Oxy-Gas Profiling |
8500 |
24000 |
170 |
Large size plate processing inc. direct edge bevelling, |
Edge finishing |
|
|
60 |
Off-line mechanical bevelling from nine machines |
Further processing can be undertaken either by Tata Steel, or with our partners, including shotblasting/priming and heat treatment.
Our Stockholder Sales team provides a dedicated competitive offering to UK stockholders - ensuring access to the full range of Tata Steel product and processing capabilities. By utilising the integrated Tata Steel supply chain and our extensive processing capability we can provide you with high-quality products when and where you need them. Products on offer include:
- wide coil
- sheets
- plate
- slits
- RMP
Competitive and convenient. To save you time and money, we offer:
Extensive capacity and products you can rely on. As the country’s largest distributor and processor of steel, our best-in-class facilities can be utilised to supply a superior quality product, manufactured by Tata Steel. Our processing capacity ensures we are able to supply the product you need on a competitive basis from our large-scale, low-cost facilities.
Product choice. As well as wide coil, we also supply decoiled sheets, slit coil and blanks - saving you cost and time in further processing.
Multi-product service. Our team is able to handle all your steel requirements - acting as a single point-of-contact for the wide product and processing capabilities available from our multiple processing hubs.
At Stockholder Sales we provide several services to support our customers and complement our comprehensive offering:
Finding the right product. We combine knowledge of Tata Steel’s products and extensive processing capability with an understanding of customer applications. We use our experience and expertise to ensure that the most appropriate solutions are offered for each enquiry.
Flexible and regular delivery. Our 24-hour supply chain operations support flexible and regular delivery schedules on a nationwide basis. Integrated IT systems allow customers to focus on their own business activities with peace of mind regarding security of supply.
More support. As part of Tata Steel, we have direct access to our own manufacturing facilities. This allows customers to benefit from increased levels of product information, technical support and material availability.
Steelpark Wednesfield fact sheet
More about the Steelpark, the UK’s largest steel distribution and processing centre, and the only one to be supported by a domestic steel mill. Based in Wednesfield, West Midlands, the Steelpark has specialised in distribution and processing for 20 years.
Steelpark visitor safety guide and information
Information for visitors to Steelpark including directions, visitor safety, meeting room information and useful contacts.
Tata Steel UK standard conditions of sale
Standard conditions of sale for deliveries worldwide effective on all orders accepted by Tata Steel Europe group companies under English law. Version date: September 2010
Quality certificates:
EN-Service centres-Contact-UK Steelpark
Steelpark
The Steelpark
Steelpark Way
Wednesfield, Wolverhampton
WV11 3SQ